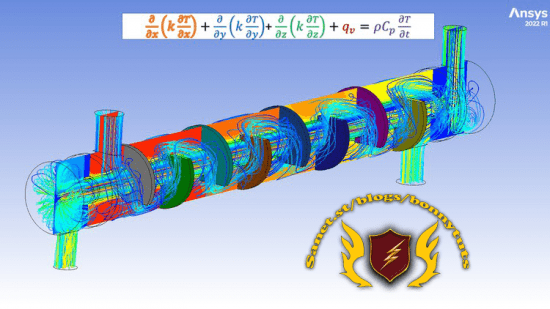
Published 09/2022
MP4 | Video: h264, 1280×720 | Audio: AAC, 44.1 KHz, 2 Ch
Genre: eLearning | Language: English | Duration: 26 lectures (6h 7m) | Size: 3.54 GB
CFD analysis of five designs of shell & tube heat exchanger in ANSYS CFD
What you’ll learn
Understanding basics of heat exchanger theory and mathematical modeling
Learn advanced level techniques in spaceclaim to create complex models
Creating geometry of Heat Exchanger with various features such as shell, tubes, side plate, side plate, baffles etc
Creating high quality grid for various components of heat exchanger in ANSYS meshing
Creating interfaces for heat transfer in ANSYS meshing
Setting up problem in Fluent such as boundary conditions, cell zones, material properties, solver settings, report definitions etc.
Solving CFD model in Fluent using coupled solver and accelerating solution using time scale factor with optimum settings
Post processing CFD results of all five designs
Mesh independence study to get the mesh that is optimum to produce good results
Comparing results with analytical calculations and accessing performance of different components of heat exchanger in enhancing heat transfer
Comparing all cases in CFD post for side by side comparison
Requirements
Basic understanding of heat transfer, heat exchangers, CFD and ANSYS CFD
Computer with i5/i7 processor and 16 GB RAM
ANSYS 2022 R1 (professional version) installed on your computer. You can use student version but you will not able to create model with more than 0.5 million cells.
Description
Heat exchangers are an integral part of many engineering systems such as power plants, process plants. Heat exchangers are used to transfer heat from high temperature to low temperature zones. Both zones can be separated or may be in direct contact. One of most widely used configuration of heat exchangers is shell & tube heat exchangers.
In this course, you will learn about the basics of heat exchangers, their types, heat transfer mechanism, temperature variation and calculations of unknown based on given information about heat exchanger. After that you will create cad model of various design of shell and tube heat exchanger in spaceclaim. They design approach used in this course is modular i.e. we will start with most simplest design i.e. double pipe heat exchanger and then we will add different parts such as baffles, tubes, tube bundles, tube plates, shell etc. In total we will create five design and we will check their impact on heat exchanger performance. You will also learn about creating named selections/boundary conditions in spaceclaim.
Subsequently, we will create high quality mesh of these five designs in ANSYS meshing using various approaches and methods. We will also create mesh interfaces either in ANSYS meshing or Fluent which ever is more efficient of doing so. Boundary layer meshing is also discussed to capture important flow features and heat transfer in heat exchanger.
After that, mesh will imported into Fluent automatically using workbench interface. We will setup problem in Fluent by providing turbulence model, energy equation, materials such as water liquid and copper, cell zone conditions, boundary conditions for shell inlet and tube inlet, report definitions, mesh interfaces, solver settings. You will also about the solution initializing, solution convergence acceleration using time scale factor etc.
Once CFD simulation is solved and fully converged, we will extract results such as pressure, temperature and velocity contours. We will also find out temperatures at the shell and tube outlet and compare them among five designs and also with analytical results. We will also compare all five design in CFD-Post to get the complete picture of effect of various designs parameters on heat exchanger flow field and heat transfer.
Please note, we will use ANSYS 2022 R1. Therefore please install it on your computer before starting this course. You can also use ANSYS student version but the cell count limit is 512 K cells.
Who this course is for
Students and professionals who want to learn advanced CFD modeling for heat transfer systems especially heat exchangers
Password/解压密码www.tbtos.com